Operational Excellence Model, Lean Manufacturing Tools & Traceability Systems. Great principles great implementation, better products.
OUR OPERATIONAL EXCELLENCE MODEL
Our Operational Excellence Model is based in the Toyota Production System (TPS) and The Shingo model, and is the relentless pursuit of improvement through a challenging mindset that must prevail across the entire organization connecting and aligning principle based behaviors with business results, focusing in production control, quality, maintenance, customer service and personnel growth.
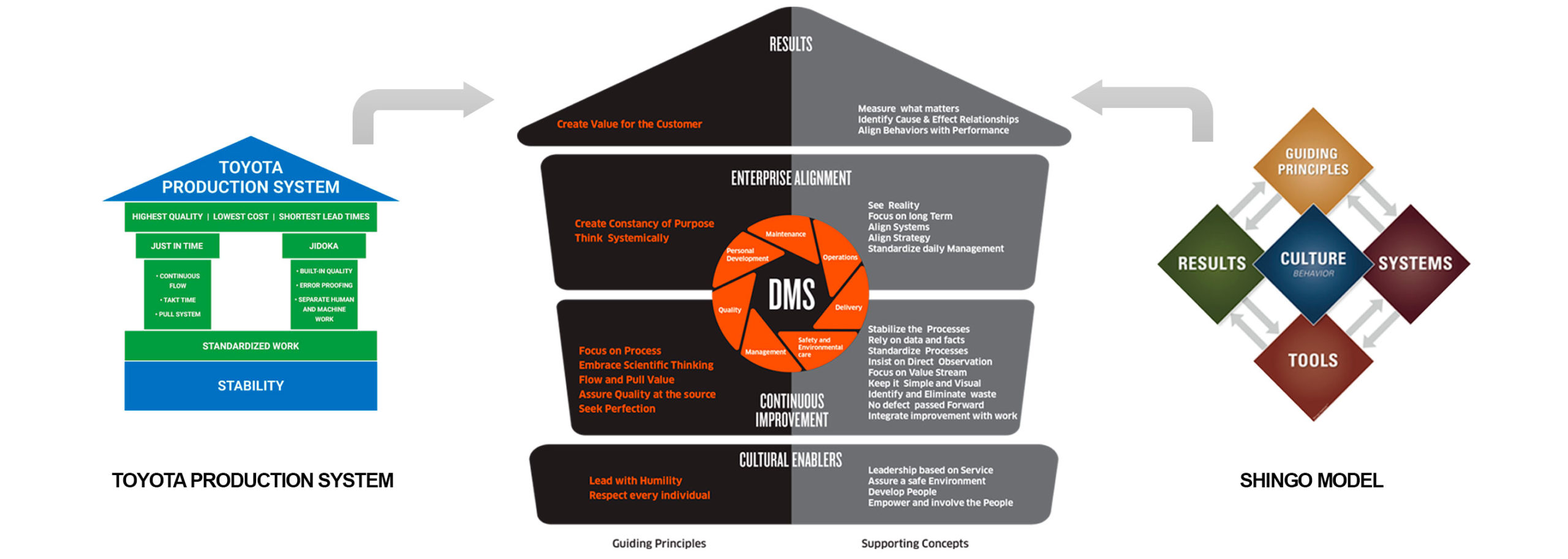
Now you know, this is how we do it
LEAN MANUFACTURING TOOLS
Lean manufacturing tools is a set of techniques, methods and concepts, each one designed to achieve a particular goal within a manufacturing environment, so there are operation stabilization tools, tools for continuous improvement and tools for intensive improvement, there are also methods to find the root cause of problems and follow-up techniques to monitor performance, by using them all in a manufacturing facility it is possible to build a high performance improvement system, thus achieving Operational Excellence.
PSTBR
Principles Systems Tools Behaviors and Results
It’s purpose is to create excellence in the organization through the application of universal principles for operational excellence, aligning management systems, and the correct application of improvement techniques throughout the organization, thus achieving a culture of sustainable excellence based on principles.
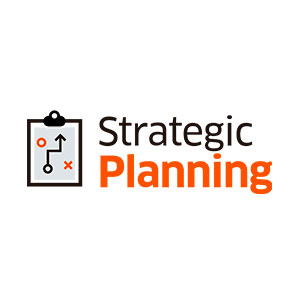
STRATEGIC PLANNING
It is a structured process to develop, translate and align short-term action programs with strategic and multi-functional priorities.
Strategy development occurs by defining strategic objectives, indicators, goals, initiatives, and budgets that guide action and the allocation of resources.
VSM
A graphic technique that allows visualizing an entire process, detailing and fully understanding the flow of both information and materials necessary for a product or service to reach the customer, besides, waste and activities that do not add value to the process are identified to subsequently start activities for disposal.
5S
It is a system whose philosophy is to organize work areas in an agile, safe, and efficient way so that waste is minimized, focusing on building a quality environment for the organization, ensuring alignment to standards for continuous improvement.
JIDOKA ANDON
It is an active procedure that must be carried out by the personnel responsible for the area in the event of faults or problems detected in the processes that affect compliance with the production plan, quality, and deliveries to the client.
A1
It is a set of activities and records in a determined period, defined by a production standard that allows the stabilization of processes.
SDCA
It is a standardization and continuous improvement strategy in four steps to stabilize an operation or service system.
SDCA stands for (STANDARDIZE DO CHECK ACT)
WATER SPIDER
It is a function in charge of maintaining a continuous process flow by supplying materials according to the production schedule and Kanban.
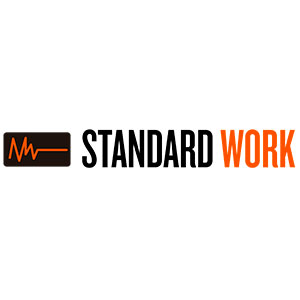
STANDARD WORK
It is a methodology that guarantees repetition, quality and planned productivity considering installed production capacities and jobs involved, it serves as a basis for personal development and a drive for continuous improvement.
SMED
It is a process of continuous improvement that achieves the reduction, standardization, and stabilization of the time of design change in production processes, by eliminating or reducing waste represented as activities during design changes.
KANBAN
It is a visual information system, which controls the manufacture or supply of the necessary products in the quantity required by the production line.
3G+K
It is an improvement system made up of a set of tools that aims to display key metrics of our processes to all personnel, simply and visually, and to promote improvement as a result of direct observation.
PDCA-A3
It is a strategy of continuous improvement in four simple steps that allows you to make a change by identifying, analyzing and following up on the solution of a problem.
PDCA stands for PLAN - DO - CHECK - ACT.
A2
It is a creative solution in order to solve, minimize or eliminate the root cause of a problem that is considered relatively easy to compound.
EVENTO KAIZEN
It is a program of Intensive Improvement Events derived from VSM, Strategic Planning, Monthly Management Review, 3G + K Agenda, etc. It is aligned to the plant and business strategies for the execution of actions in the short term with a high impact in a positive and significant in the key indicators.
DOJO
DOJO is a Japanese word that means space for practice, teaching and training.
At Deacero Summit we dedicate a space to teach - learn, apply and practice a series of principles, tools, and methods as a part of our Operational Excellence Strategy.
MEDAT
MEDAT is our systematic application tool, designed to validate the correct processing of wire rod in the drawing machines of the Deacero Group and external clients.
MEDAT is an acronym for Wire Drawing Performance Evaluation Model in the organization.
TRACEABILITY SYSTEM
Production never stops
so you will know where
it is…all the time.
so you will know where
it is…all the time.
Our Traceability Standard will maximize usage of the well-established, globally acceptable supply chain standards that uniquely identify a “traceable item”, describe the establishment of appropriate and effective records of events, and provides for accurate communication about the traceable item between Customers / Suppliers / Partners.
This meets the core need to be able to track forward and trace back at any point along the full supply chain no matter how many traceability partners and business process steps are involved.
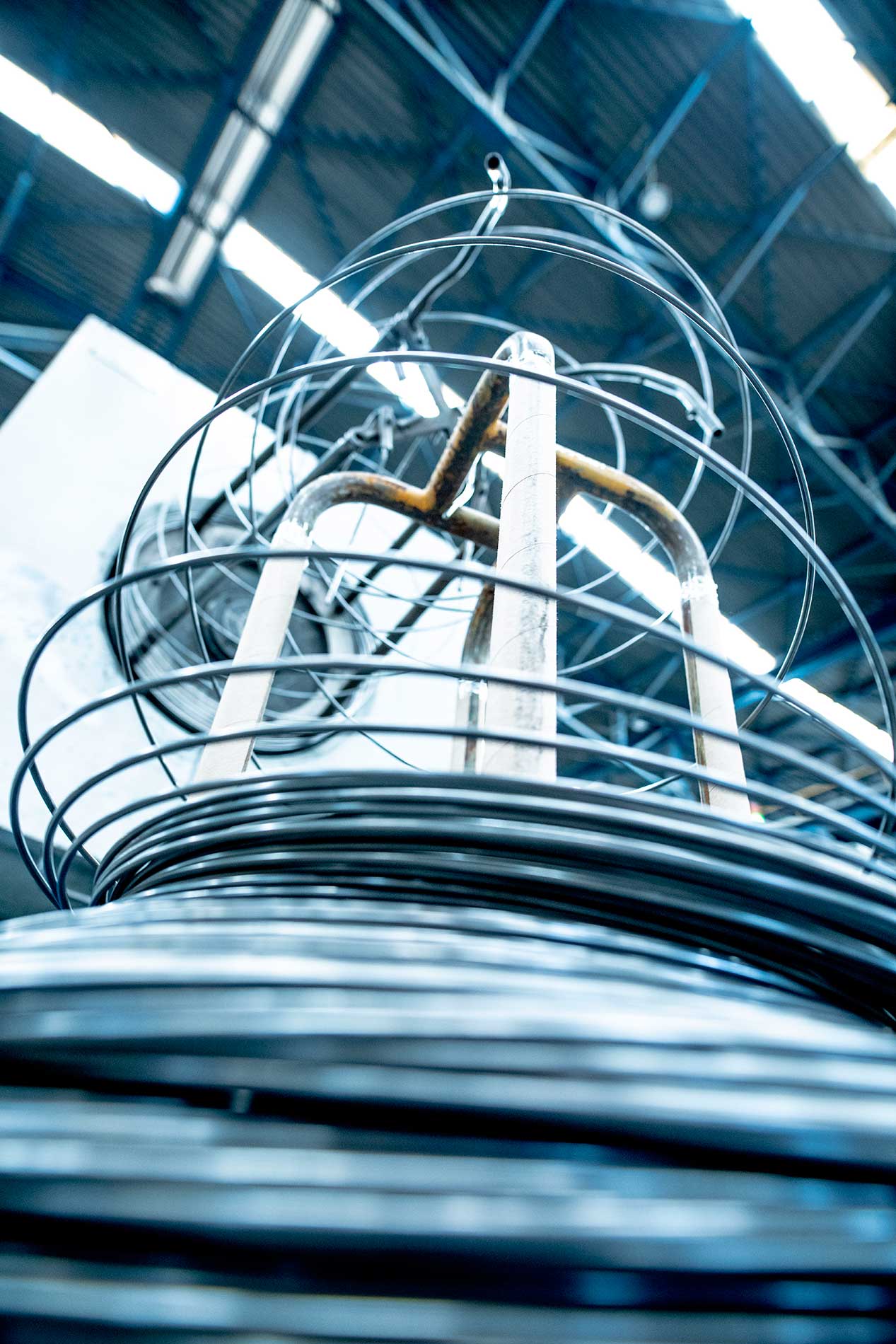
Work in process (WIP) Records
- 100% Special control system for Heat Treatment process, tests results. Dimensional, Physical and Mechanical
- All records and results are kept in our system
- History of every OPM (production order) is stored in our system
- 1. Pickling & Coating (phosphate, borax, lime, lube or polymer)
- 2. Drawing
- 3. Furnace
- 4. Release from quality inspection
- 5. Pickling & Coating (phosphate, borax, lime, lube or polymer)
- 6. Drawing
- 7. Release from quality inspection
- 8. Packaging
- 9. Finished Product